Sklejka składa się z trzech lub więcej cienkich warstw drewna połączonych ze sobą klejem. Każda warstwa drewna, lub sklejka, jest zazwyczaj zorientowana tak, aby jej słoje biegły pod kątem prostym do sąsiedniej warstwy, aby zmniejszyć skurcz i poprawić wytrzymałość gotowego elementu. Większość sklejki jest prasowana w duże, płaskie arkusze stosowane w budownictwie. Inne kawałki sklejki mogą być formowane w proste lub złożone krzywe do wykorzystania w meblach, łodziach i samolotach.
Stosowanie cienkich warstw drewna jako środka konstrukcyjnego datuje się na około 1500 r. p.n.e., kiedy egipscy rzemieślnicy połączyli cienkie kawałki ciemnego drewna hebanowego z zewnętrzną częścią trumny cedrowej znalezionej w grobowcu króla Tutanchamona. Tę technikę później stosowali Grecy i Rzymianie do produkcji pięknych mebli i innych przedmiotów dekoracyjnych. W latach 1600. sztuka dekorowania mebli cienkimi kawałkami drewna stała się znana jako fornirowanie, a same elementy stały się znane jako forniry.
Do końca XVIII wieku kawałki forniru były wycinane wyłącznie ręcznie. W 1797 roku Anglik Sir Samuel Bentham złożył wniosek patentowy na kilka maszyn do produkcji forniru. W swoich wnioskach patentowych opisał koncepcję laminowania kilku warstw forniru klejem w celu utworzenia grubszego kawałka — pierwszy opis tego, co obecnie nazywamy sklejką.
Pomimo tego rozwoju minęło prawie sto lat, zanim laminowane forniry znalazły zastosowanie komercyjne poza przemysłem meblarskim. Około 1890 roku laminowane drewno zostało po raz pierwszy użyte do budowy drzwi. Wraz ze wzrostem popytu, kilka firm zaczęło produkować arkusze wielowarstwowego laminowanego drewna, nie tylko do drzwi, ale także do stosowania w wagonach kolejowych, autobusach i samolotach. Pomimo tego zwiększonego wykorzystania, koncepcja stosowania „klejonego drewna”, jak sarkastycznie nazywali je niektórzy rzemieślnicy, wygenerowała negatywny wizerunek produktu. Aby przeciwdziałać temu wizerunkowi, producenci laminowanego drewna spotkali się i ostatecznie ustalili termin „sklejka”, aby opisać nowy materiał.
W 1928 roku w Stanach Zjednoczonych wprowadzono pierwsze standardowe arkusze sklejki o wymiarach 4 ft x 8 ft (1,2 m x 2,4 m) do użytku jako ogólny materiał budowlany. W kolejnych dekadach ulepszone kleje i nowe metody produkcji pozwoliły na wykorzystanie sklejki w szerokim zakresie zastosowań. Obecnie sklejka zastąpiła tarcicę ciętą w wielu celach budowlanych, a produkcja sklejki stała się wielomiliardowym, światowym przemysłem.
Zewnętrzne warstwy sklejki są znane odpowiednio jako lico i tył. Lico to powierzchnia, która ma być używana lub widoczna, podczas gdy tył pozostaje nieużywany lub ukryty. Środkowa warstwa jest znana jako rdzeń. W sklejkach z pięcioma lub większą liczbą warstw, warstwy pośrednie są znane jako pasy poprzeczne.
Sklejka może być wykonana z drewna liściastego, iglastego lub z połączenia obu. Niektóre popularne gatunki drewna liściastego to jesion, klon, mahoń, dąb i tek. Najczęściej używanym drewnem iglastym do produkcji sklejki w Stanach Zjednoczonych jest jodła Douglasa, chociaż używa się również kilku odmian sosny, cedru, świerka i sekwoi.
Sklejka kompozytowa ma rdzeń wykonany z płyty wiórowej lub litego drewna łączonego krawędź do krawędzi. Wykończona jest fornirem ze sklejki na stronie przedniej i tylnej. Sklejka kompozytowa jest stosowana tam, gdzie potrzebne są bardzo grube arkusze.
Rodzaj kleju używanego do łączenia warstw drewna zależy od konkretnego zastosowania gotowej sklejki. Arkusze sklejki z drewna iglastego przeznaczone do montażu na zewnątrz konstrukcji zazwyczaj wykorzystują żywicę fenolowo-formaldehydową jako klej ze względu na jej doskonałą wytrzymałość i odporność na wilgoć. Arkusze sklejki z drewna iglastego przeznaczone do montażu wewnątrz konstrukcji mogą wykorzystywać klej z białkiem krwi lub białkiem sojowym, chociaż większość wewnętrznych arkuszy z drewna iglastego jest obecnie wytwarzana z tej samej żywicy fenolowo-formaldehydowej, która jest stosowana do arkuszy zewnętrznych. Sklejka z drewna liściastego stosowana do zastosowań wewnętrznych i w konstrukcji mebli zazwyczaj jest wytwarzana z żywicy mocznikowo-formaldehydowej.
Niektóre zastosowania wymagają arkuszy sklejki, które mają cienką warstwę plastiku, metalu lub impregnowanego żywicą papieru lub tkaniny przyklejonej do powierzchni lub spodu (lub obu), aby nadać zewnętrznej powierzchni dodatkową odporność na wilgoć i ścieranie lub poprawić jej właściwości zatrzymywania farby. Taka sklejka nazywana jest sklejką nakładaną i jest powszechnie stosowana w budownictwie, transporcie i rolnictwie.
Inne arkusze sklejki mogą być pokrywane płynną bejcą, aby nadać powierzchni wykończony wygląd, lub mogą być poddawane działaniu różnych środków chemicznych w celu zwiększenia ognioodporności sklejki lub jej odporności na gnicie.
Istnieją dwie główne klasy sklejki, z których każda ma swój własny system klasyfikacji.
Jedna klasa jest znana jako budowlana i przemysłowa. Sklejki w tej klasie są używane głównie ze względu na ich wytrzymałość i są oceniane według ich zdolności do ekspozycji i klasy forniru użytego na wierzchu i spodzie. Zdolność do ekspozycji może być wewnętrzna lub zewnętrzna, w zależności od rodzaju kleju. Klasy forniru mogą być N, A, B, C lub D. Klasa N ma bardzo mało wad powierzchni, podczas gdy klasa D może mieć liczne sęki i pęknięcia. Na przykład sklejka używana do podłóg w domu jest oceniana jako „Wewnętrzna CD”. Oznacza to, że ma powierzchnię C z spodem D, a klej nadaje się do stosowania w chronionych miejscach. Wewnętrzne warstwy wszystkich sklejek budowlanych i przemysłowych są wykonane z forniru klasy C lub D, niezależnie od oceny.
Inna klasa sklejki znana jest jako twarda i dekoracyjna. Sklejki w tej klasie są używane głównie ze względu na swój wygląd i są klasyfikowane w kolejności malejącej odporności na wilgoć jako Technical (Exterior), Type I (Exterior), Type II (Interior) i Type III (Interior). Ich forniry są praktycznie wolne od wad.
Rozmiary
Grubość arkuszy sklejki waha się od 0,06 cala (1,6 mm) do 3,0 cala (76 mm). Najczęściej spotykane grubości mieszczą się w zakresie od 0,25 cala (6,4 mm) do 0,75 cala (19,0 mm). Chociaż rdzeń, pasy poprzeczne oraz powierzchnia i tył arkusza sklejki mogą być wykonane z fornirów o różnej grubości, grubość każdego z nich musi być zrównoważona w środku. Na przykład powierzchnia i tył muszą mieć równą grubość. Podobnie górne i dolne pasy poprzeczne muszą być równe.
Najczęściej spotykany rozmiar arkuszy sklejki wykorzystywanych w budownictwie to 4 stopy (1,2 m) szerokości i 8 stóp (2,4 m) długości. Inne popularne szerokości to 3 stopy (0,9 m) i 5 stóp (1,5 m). Długości wahają się od 8 stóp (2,4 m) do 12 stóp (3,6 m) w odstępach co 1 stopę (0,3 m). Specjalne zastosowania, takie jak budowa łodzi, mogą wymagać większych arkuszy.
Drzewa używane do produkcji sklejki są na ogół mniejsze w średnicy niż te używane do produkcji drewna. W większości przypadków są sadzone i uprawiane na obszarach należących do firmy produkującej sklejkę. Obszary te są starannie zarządzane w celu maksymalizacji wzrostu drzew i minimalizacji szkód spowodowanych przez owady lub ogień.
Oto typowa sekwencja operacji przetwarzania drzew na standardowe arkusze sklejki o wymiarach 4 na 8 stóp (1,2 na 2,4 m):
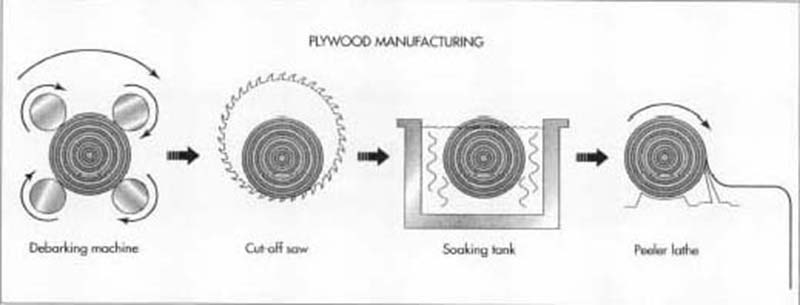
Kłody są najpierw okorowywane, a następnie cięte na bloki do obierania. Aby pociąć bloki na paski forniru, są one najpierw moczone, a następnie obierane na paski.
1 Wybrane drzewa na danym obszarze są oznaczane jako gotowe do ścięcia lub ścięcia. Ścinanie może odbywać się za pomocą pił łańcuchowych napędzanych benzyną lub dużych nożyc hydraulicznych zamontowanych z przodu pojazdów kołowych zwanych ścinaczami. Gałęzie są usuwane z powalonych drzew za pomocą pił łańcuchowych.
2 Przycięte pnie drzew, czyli kłody, są ciągnięte do miejsca załadunku przez pojazdy kołowe zwane skidderami. Kłody są cięte na długość i ładowane na ciężarówki w celu transportu do tartaku, gdzie są układane w długie stosy zwane pokładami kłód.
3 Gdy kłody są potrzebne, są one podnoszone z pokładów przez ładowarki na gumowych oponach i umieszczane na przenośniku łańcuchowym, który dostarcza je do maszyny do korowania. Maszyna ta usuwa korę, albo za pomocą ostrych kół szlifierskich, albo za pomocą strumieni wody pod wysokim ciśnieniem, podczas gdy kłoda jest powoli obracana wokół swojej długiej osi.
4 Okorowane kłody są transportowane do młyna na przenośniku łańcuchowym, gdzie ogromna piła tarczowa tnie je na sekcje o długości od 8 stóp do 4 cali (2,5 m) do 8 stóp do 6 cali (2,6 m), nadające się do produkcji standardowych arkuszy o długości 8 stóp (2,4 m). Te sekcje kłód są znane jako bloki peeler.
5 Zanim fornir będzie mógł zostać pocięty, bloki do obierania muszą zostać podgrzane i namoczone, aby zmiękczyć drewno. Bloki mogą być gotowane na parze lub zanurzane w gorącej wodzie. Proces ten trwa od 12 do 40 godzin w zależności od rodzaju drewna, średnicy bloku i innych czynników.
6 Podgrzane bloki obieraczki są następnie transportowane do tokarki obieraczki, gdzie są automatycznie wyrównywane i podawane do tokarki pojedynczo. Gdy tokarka obraca blok szybko wokół swojej długiej osi, ostrze noża o pełnej długości obiera ciągły arkusz forniru z powierzchni obracającego się bloku z szybkością 300-800 stóp/min (90-240 m/min). Gdy średnica bloku zmniejszy się do około 3-4 cali (230-305 mm), pozostały kawałek drewna, znany jako rdzeń obieraczki, jest wyrzucany z tokarki, a na jego miejsce podawany jest nowy blok obieraczki.
7 Długi arkusz forniru wyłaniający się z / tokarki do obierania może być natychmiast przetwarzany lub może być przechowywany w długich, wielopoziomowych tacach lub nawijany na rolki. W każdym przypadku następny proces obejmuje cięcie forniru na użyteczne szerokości, zwykle około 4 stóp-6 cali (1,4 m), w celu wykonania standardowych arkuszy sklejki o szerokości 4 stóp (1,2 m). Jednocześnie skanery optyczne szukają sekcji z niedopuszczalnymi defektami i są one wycinane, pozostawiając kawałki forniru o szerokości mniejszej niż standardowa.
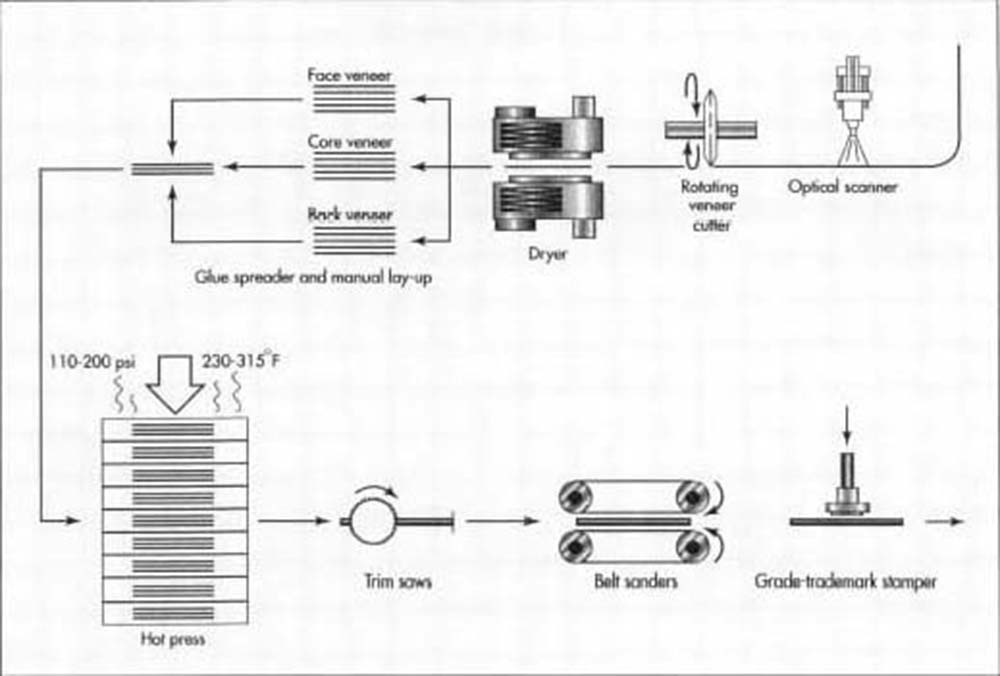
Mokre paski forniru są zwijane w rolkę, podczas gdy skaner optyczny wykrywa wszelkie niedopuszczalne wady drewna. Po wysuszeniu fornir jest sortowany i układany w stosy. Wybrane sekcje forniru są sklejane ze sobą. Gorąca prasa jest używana do uszczelnienia forniru w jeden solidny kawałek sklejki, który zostanie przycięty i przeszlifowany przed wytłoczeniem odpowiedniej klasy.
8 Sekcje forniru są następnie sortowane i układane według gatunku. Może to być wykonywane ręcznie lub automatycznie przy użyciu skanerów optycznych.
9 Posortowane sekcje są wprowadzane do suszarki, aby zmniejszyć ich zawartość wilgoci i umożliwić im skurczenie się przed sklejeniem. Większość fabryk sklejki używa mechanicznej suszarki, w której elementy poruszają się nieprzerwanie przez ogrzewaną komorę. W niektórych suszarkach strumienie ogrzanego powietrza o dużej prędkości są wdmuchiwane na powierzchnię elementów, aby przyspieszyć proces suszenia.
10 Gdy sekcje forniru wychodzą z suszarki, są układane według gatunku. Sekcje podszerokościowe mają dodatkową warstwę forniru łączoną taśmą lub klejem, aby elementy nadawały się do stosowania w warstwach wewnętrznych, gdzie wygląd i wytrzymałość są mniej ważne.
11. Te części forniru, które będą instalowane poprzecznie — rdzeń w przypadku arkuszy trzywarstwowych lub pasy poprzeczne w przypadku arkuszy pięciowarstwowych — są cięte na odcinki o długości około 4 stóp i 3 cali (1,3 m).
12 Gdy odpowiednie sekcje forniru zostaną zmontowane dla konkretnego przebiegu sklejki, rozpoczyna się proces układania i sklejania elementów. Może to być wykonywane ręcznie lub półautomatycznie za pomocą maszyn. W najprostszym przypadku arkuszy trójwarstwowych, fornir tylny jest układany płasko i przepuszczany przez rozprowadzacz kleju, który nakłada warstwę kleju na górną powierzchnię. Krótkie sekcje forniru rdzeniowego są następnie układane poprzecznie na wierzchu sklejonego tyłu, a cały arkusz jest przepuszczany przez rozprowadzacz kleju po raz drugi. Na koniec fornir wierzchni jest układany na wierzchu sklejonego rdzenia, a arkusz jest układany z innymi arkuszami czekającymi na włożenie do prasy.
13 Sklejone arkusze są ładowane do wielootworowej prasy na gorąco. Prasy mogą obsługiwać 20-40 arkuszy na raz, przy czym każdy arkusz jest ładowany w oddzielnym gnieździe. Gdy wszystkie arkusze są załadowane, prasa ściska je razem pod ciśnieniem około 110-200 psi (7,6-13,8 bara), jednocześnie podgrzewając je do temperatury około 230-315° F (109,9-157,2° C). Ciśnienie zapewnia dobry kontakt między warstwami forniru, a ciepło powoduje prawidłowe utwardzenie kleju dla maksymalnej wytrzymałości. Po upływie 2-7 minut prasa jest otwierana, a arkusze są rozładowywane.
14 Następnie surowe arkusze przechodzą przez zestaw pił, które przycinają je do ostatecznej szerokości i długości. Wyższej jakości arkusze przechodzą przez zestaw szlifierek taśmowych o szerokości 4 stóp (1,2 m), które szlifują zarówno powierzchnię czołową, jak i tylną. Arkusze średniej jakości są ręcznie szlifowane punktowo w celu oczyszczenia szorstkich obszarów. Niektóre arkusze są przepuszczane przez zestaw tarcz piły tarczowej, które wycinają płytkie rowki na powierzchni czołowej, aby nadać sklejce fakturowany wygląd. Po ostatecznej inspekcji wszelkie pozostałe wady są naprawiane.
15 Gotowe arkusze są ostemplowane znakiem towarowym klasy, który podaje kupującemu informacje o ocenie ekspozycji, klasie, numerze młyna i innych czynnikach. Arkusze o tym samym znaku towarowym klasy są łączone w stosy i przenoszone do magazynu w oczekiwaniu na wysyłkę.
Podobnie jak w przypadku drewna, nie ma czegoś takiego jak idealny kawałek sklejki. Wszystkie kawałki sklejki mają pewną liczbę wad. Liczba i lokalizacja tych wad określa gatunek sklejki. Normy dla sklejek budowlanych i przemysłowych są definiowane przez Product Standard PS1, opracowaną przez National Bureau of Standards i American Plywood Association. Normy dla sklejek liściastych i dekoracyjnych są definiowane przez ANSIIHPMA HP, opracowaną przez American National Standards Institute i Hardwood Plywood Manufacturers' Association. Normy te nie tylko ustanawiają systemy klasyfikacji sklejki, ale także określają kryteria konstrukcyjne, wydajnościowe i zastosowania.
Mimo że sklejka dość efektywnie wykorzystuje drewno — zasadniczo rozkładając je i składając z powrotem w mocniejszą, bardziej użyteczną konfigurację — w procesie produkcyjnym nadal występuje znaczna ilość odpadów. W większości przypadków tylko około 50–75% użytecznej objętości drewna w drzewie jest przetwarzane na sklejkę. Aby poprawić tę liczbę, opracowywanych jest kilka nowych produktów.
Jednym z nowych produktów jest płyta o wiórach zorientowanych, która powstaje przez rozdrobnienie całego kłody na pasma, zamiast zrywania forniru z kłody i usuwania rdzenia. Pasma są mieszane z klejem i kompresowane w warstwy, w których słoje biegną w jednym kierunku. Te skompresowane warstwy są następnie zorientowane pod kątem prostym do siebie, jak sklejka, i są ze sobą łączone. Płyta o wiórach zorientowanych jest tak samo wytrzymała jak sklejka i kosztuje nieco mniej.
Czas publikacji: 10-08-2021